
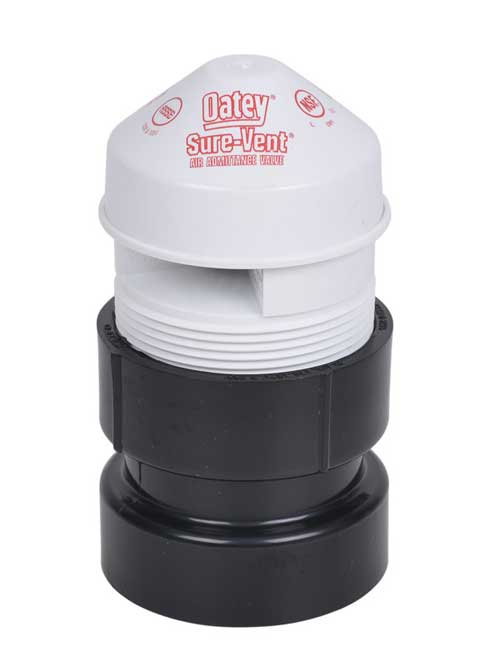
- #Air admittance valve problems with no main vent install
- #Air admittance valve problems with no main vent full
This provides accurate data to assist in understanding the pressure characteristics of the steam passing through the steam heat exchanger.
#Air admittance valve problems with no main vent install
It’s a good practice to install a pressure gauge before and after a control valve and on the condensate return leg after the steam trap. Pressure gauges provide the information necessary to understand the conditions inside the system.
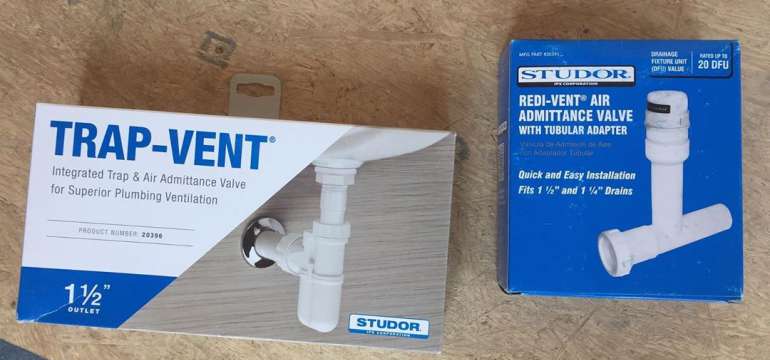
Install pressure gauges before and after the control valve Incorrectly sized control valves can lead to poor process temperature control, premature wear of the valve seats and excessive noise. Regulating valve = 20:1 turndown ratio.Globe control valve = 30:1 turndown ratio.Cage control = 40:1 turndown ratio provides the highest degree of controllability.A primary factor in selecting control valves is the turndown capability, rangeability or working range of the valve.Īll valves will have a certain amount of uncontrollable flow, particularly at the extreme ranges of the valve stroke due to sealing tolerances and linearity of flow.įollowing are some turndown ratio guidelines for control valves: Heat transfer components require properly sized control valves for effective process temperature control and seat life. Follow turndown ratio guidelines for control valves These methods either prevent condensation in the first place or allow the condensate to be diverted away from the control valve to be evacuated with the assistance of a steam trap. Installing a drip leg prior to the valve, insulation improvement, correctly grading the steam line, or installation of a steam separator prior to the valve are just some of the methods. You can eliminate the build-up of condensate in a number of ways. Additionally, any condensate passing through the steam control valve can cause premature failure of the control valve. Condensate accumulation before the valve can cause a water hammer. At low or no flow scenarios, condensate can accumulate prior to the inlet of the control valve. Eliminate steam supply condensate build-up and carryoverĪ steam control valve is designed to modulate steam flow between 0 to 100%. The following best practices listed throughout this article should be reviewed and implemented in your facility’s steam system design, maintenance, and specification program prior to selecting your next steam heat exchanger and tracing components. Example problems include:įollowing some simple guidelines and proven field techniques can help you avoid the common problems associated with designing an industrial steam system. The experts at Swagelok have reviewed numerous industrial heat transfer applications in various locations and industries and have found the most common problems are caused by either incorrect component selection or improper installation practices. Register for Swagelok’s Steam Services Training Course Common Design and Product Selection Issuesīasic fundamentals must be considered when designing an industrial steam system to avoid premature failure or under performance. Failing to understand the context of the application commonly results in inappropriate control or selection of system components. A thorough review should be conducted of the steam system’s operating parameters and documentation. Inadequate performance is most commonly attributed to a design engineer’s failure to consider all steam system characteristics.
#Air admittance valve problems with no main vent full
Steam Heat Exchangers and Tracing Systems: Best Practices for Design EngineersĪlex Chu, Industrial Steam System SME, Swagelok Field Engineeringĭesigning a proper steam heat exchanger or steam heat tracing system first requires a full understanding of the operational characteristics where the system will function.
